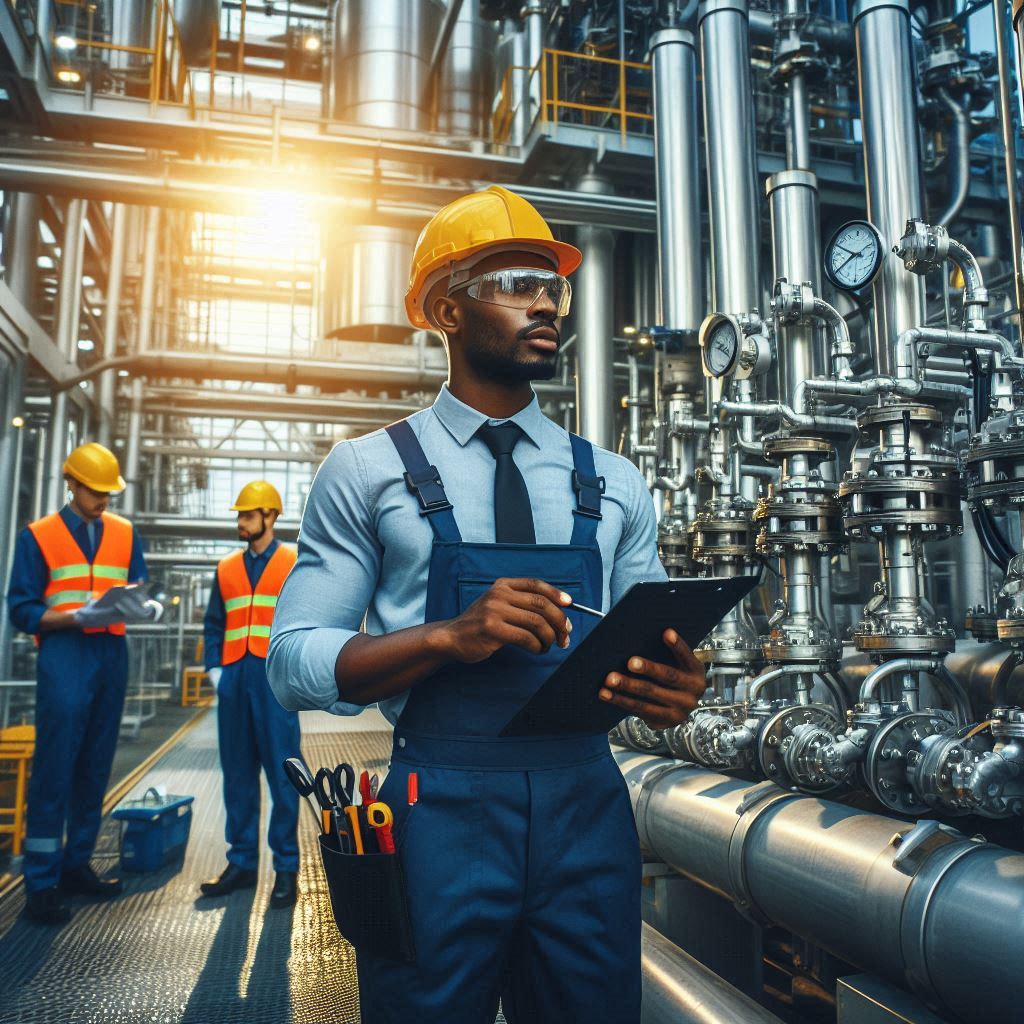
Quando um cliente solicita um orçamento para um projeto industrial, é costume que ele faça isso para várias empresas de engenharia ao mesmo tempo. Na necessidade de ser rápido para vencer os concorrentes, mas ao mesmo tempo ser acurado o bastante para projetar custos, surge uma pergunta: quantas válvulas um processo químico utiliza? Quantas válvulas de controle? E quantas válvulas de segurança?
Hoje:
- discutiremos o papel das válvulas de controle, segurança e bloqueio;
- discutiremos a importância do projeto básico para o empreendedor e compararemos dois projetos de processos químicos;
- aplicaremos as conclusões da comparação dos projetos em um exemplo, para validar a acurácia dos resultados obtidos.
Tabela de Conteúdo
O papel das válvulas na indústria
Na indústria de processos químicos, todo processo, em alguma extensão, se utiliza da manipulação de fluidos, sejam eles líquidos ou gasosos.
Para que esses fluidos exerçam o papel desejado ou sofram as transformações necessárias, é necessário controle das variáveis controladas (como temperatura) e das variáveis manipuladas (como a vazão). Logo, as válvulas de controle são componentes vitais de toda indústria de processos químicos.
Ao mesmo tempo, é necessário se preocupar com a integridade do patrimônio do ativo industrial, dos funcionários que trabalham no local, e com o meio ambiente e as comunidades no entorno, pois, um erro ou falha na manipulação dessas variáveis pode trazer consequências de prejuízos incalculáveis. Pense numa panela de pressão em mau estado de conservação.
Logo, válvulas de segurança e alívio são componentes típicos e também críticos para um processo químico.
Por último, como tudo na vida tem um fim, e como imprevistos sempre são previsíveis, muitas vezes ao longo da campanha da planta serão necessárias paradas parciais ou totais para reposição ou manutenção de peças e equipamentos inteiros.
Para que isso ocorra, é necessário garantir o acesso seguro do operador aos equipamentos, canalizando fluidos quentes, pressurizados e tóxicos que possam estar acumulados em tubulações, instrumentos e vasos de pressão para os locais apropriados.
Assim, surge a necessidade de uma quantidade grande de válvulas para bloqueio das entradas e saídas dos equipamentos, drenos e vents.
Projeto Básico e a Decisão Final de Investimento
No mercado, existe um acrônimo conhecido entre empresas do setor industrial, o FID, sigla em inglês que significa Decisão Final de Investimento.
Durante o desenvolvimento de um novo projeto, é comum que o gerente do projeto responsável pegue tudo o que foi desenvolvido até então, apresente para os tomadores de decisão (que pode ser o conselho administrativo da empresa, os diretores executivos, etc.) que então aprovam ou reprovam a decisão de continuar investindo no projeto em questão.
Digo continuar investindo porque até que este momento chegue, um montante considerável foi provisionado para estudos de viabilidade, consultorias, pesquisas de mercado, obtenção de licenças, entre muitas outras possibilidades.
Entretanto, como a compra dos materiais, equipamentos, construção e comissionamento da planta está ordens de grandeza acima em termos de custos, é bem comum que um Projeto Básico seja a etapa decisiva para a tomada de decisão, pois, nesta fase de desenvolvimento, tudo o que deverá ser construído já foi mapeado e dimensionado.
Quantas válvulas existem num projeto básico?
Eu selecionei algumas folhas de P&ID’s de dois projetos básicos de engenharia de processos que possuo em meu acervo pessoal, e contabilizei válvula por válvula, realçando válvulas de controle, válvulas de segurança, e o total, considerando aí as válvulas de bloqueio (também considerei válvulas de retenção neste grupo).
O primeiro, é de produção de triclorossilano e posterior deposição química do silício. O segundo, é para produção de metanol (a partir do gás natural).
Os resultados obtidos foram os seguintes:
Triclorossilano:
Área | folha | Número de Equipamentos | Número de válvulas de controle | Número de PSVs | Número Total de Válvulas | Número de válvulas por equipamento | número de válvulas de controle por equipamento | Número de PSVs por equipamento |
100 | 1 | 10 | 6 | 4 | 235 | 23.50 | 0.60 | 0.40 |
100 | 2 | 3 | 1 | 0 | 52 | 17.33 | 0.33 | 0.00 |
200 | 1 | 4 | 4 | 7 | 151 | 37.75 | 1.00 | 1.75 |
300 | 1 | 3 | 1 | 4 | 67 | 22.33 | 0.33 | 1.33 |
300 | 2 | 5 | 4 | 6 | 131 | 26.20 | 0.80 | 1.20 |
400 | 1 | 6 | 2 | 4 | 130 | 21.67 | 0.33 | 0.67 |
400 | 3 | 2 | 4 | 2 | 80 | 40.00 | 2.00 | 1.00 |
400 | 4 | 6 | 7 | 2 | 181 | 30.17 | 1.17 | 0.33 |
Média | 27.37 | 0.82 | 0.84 |
Metanol:
Área | folha | Número de Equipamentos | Número de válvulas de controle | Número de PSVs | Número Total de Válvulas | Número de válvulas por equipamento | número de válvulas de controle por equipamento | Número de PSVs por equipamento |
100 | 1 | 13 | 3 | 2 | 118 | 9.08 | 0.23 | 0.15 |
200 | 1 | 8 | 6 | 8 | 148 | 18.50 | 0.75 | 1.00 |
200 | 2 | 5 | 6 | 3 | 71 | 14.20 | 1.20 | 0.60 |
300 | 2 | 11 | 7 | 11 | 203 | 18.45 | 0.64 | 1.00 |
400 | 1 | 4 | 6 | 4 | 96 | 24.00 | 1.50 | 1.00 |
400 | 2 | 8 | 6 | 10 | 152 | 19.00 | 0.75 | 1.25 |
500 | 1 | 9 | 6 | 5 | 136 | 15.11 | 0.67 | 0.56 |
Média | 16.91 | 0.82 | 0.79 |
É interessante observar que o projeto de metanol possui praticamente 10 válvulas por equipamento a menos que o projeto de triclorossilano; entretanto, o número de válvulas de controle e de válvulas de alívio são muito semelhantes. Portanto, a diferença entre os dois projetos reside nas válvulas de bloqueio.
Para que você compreenda melhor a razão subjacente a essa diferença e tome uma decisão bem informada, é preciso dizer uma característica do projeto de triclorossilano, que não é tão comum na indústria química: ao contrário do metanol, o triclorossilano não pode, em hipótese alguma, entrar em contato com água, correndo risco de explosão.
Assim, quando é necessária a liberação de uma tubulação ou equipamento, é necessário primeiro que se utilize como fluido de limpeza gás nitrogênio, e em seguida ar seco. Ao mesmo tempo, ao se preparar para voltar em operação, o equipamento deve ser pressurizado aos poucos, mas não pode haver ar ou nitrogênio na operação, portanto, deve haver uma saída dedicada a esses gases.
Estes dois aspectos adicionam muitas válvulas ao projeto, pois o fluido de limpeza extra entra pelo seu próprio anel de utilidades, e ao mesmo tempo o nitrogênio, quando for purgado do equipamento, não pode ser encaminhado para à tocha, devido à sua não-combustibilidade.
Outro aspecto que diverge nos dois projetos, é a utilização de válvulas de bloqueio e de dreno à montante e à jusante das PSV’s (os bloqueios travados abertos) no projeto de triclorossilano, algo que não foi considerado no projeto de metanol. Isto adiciona portanto quatro válvulas a cada PSV presente.
Estudo de Caso
Para por à prova os valores obtidos, vamos realizar o seguinte exercício:
Suponha que, no processo Haber-Bosch, amônia e gases incondensáveis (nitrogênio e hidrogênio não-reagidos) são encaminhados para a área de separação e reciclo. Nesta área, a corrente gasosa passa por um condensador parcial que torna a corrente bifásica, sendo a líquida rica em amônia, e a gasosa praticamente pura em nitrogênio e hidrogênio.
Para que haja a efetiva separação das fases, após passar pelo condensador, a corrente é encaminhada para um vaso de separação adiabático. Para o controle do balanço de massa, um controle de nível simples é adicionado na saída da corrente líquida. Para o controle da condição de equilíbrio termodinâmico necessária à purificação, é adicionado um controle de pressão na saída da corrente gasosa. Um controle de temperatura não é necessário no condensador pois a temperatura de supply do fluido refrigerante é constante e, ao mesmo tempo, desejamos condensar o máximo de amônia possível (os gases reciclados passarão por estágios de compressão, e quanto menor a temperatura, menor o consumo de eletricidade exigido).
Abaixo, uma ilustração do problema:
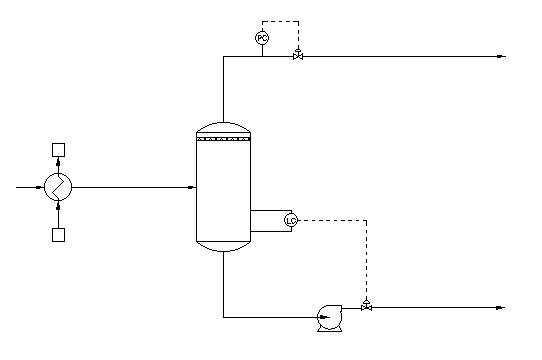
Conhecido o processo a ser desenvolvido no projeto, tenho algumas pontuações:
- É típico que haja duas bombas instaladas em paralelo, seja para manutenção sem parada, seja para operar cada uma com uma vazão menor do que a vazão total a ser desenvolvida;
- Deste modo, há quatro equipamentos neste “fluxograma”;
- Supondo um cenário de ruptura de tubo do condensador parcial, uma PSV será providenciada para o anel de utilidade, assumindo que a pressão da corrente de processo é superior à do fluido refrigerante;
- Uma PSV será responsável por limitar a sobre-pressão tanto sobre o vaso quanto sobre o trocador; uma válvula travada aberta deve ser providenciada entre esses equipamentos;
- Para bombas centrífugas, existe uma pressão máxima que esses equipamentos podem desenvolver (pressão de shut-off), sendo portanto conhecido o cenário de máxima pressão, e assim não é necessária a adição de mais uma PSV;
- Água e Nitrogênio serão utilizados como fluidos de limpeza, um por ser abundante, o outro por inertizar e pressurizar o meio com uma substância que já se encontra normalmente no processo.
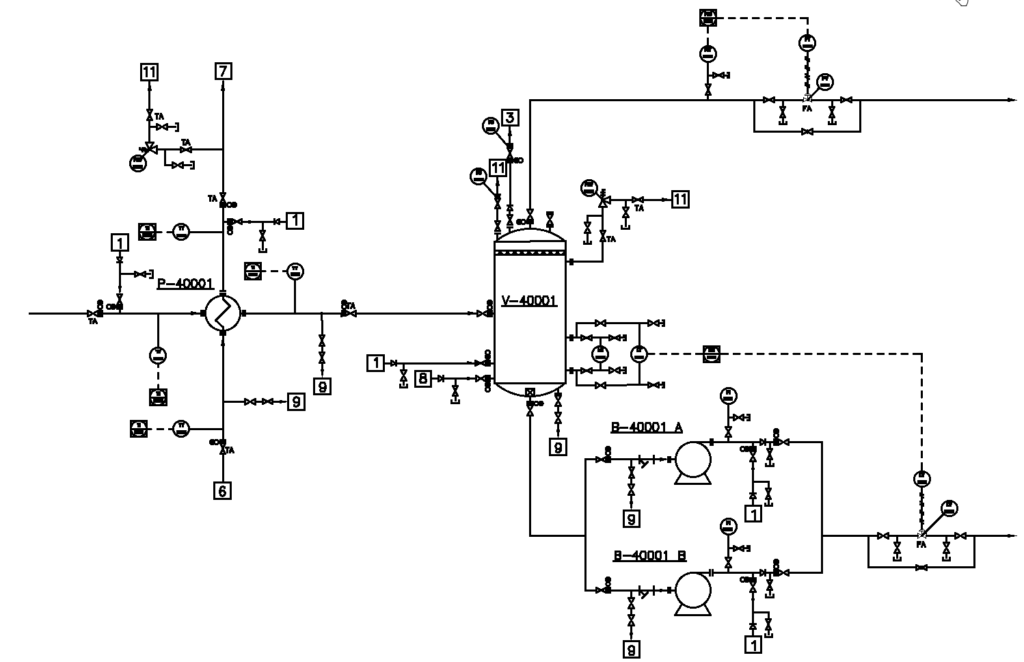
Legenda:
– 1: Água
– 11: Flare
– 3: ETG
– 6, 7: fluido refrigerante;
– 8: Nitrogênio;
– 9: ETE
Contabilizando, chegamos a:
Área | folha | Número de Equipamentos | Número de válvulas de controle | Número de PSVs | Número Total de Válvulas | Número de válvulas por equipamento | número de válvulas de controle por equipamento | Número de PSVs por equipamento |
XXX | 1 | 4 | 2 | 2 | 85 | 21.25 | 0.50 | 0.50 |
Podemos ver que, na média global, o número de válvulas por equipamento ficou dentro do range obtido anteriormente;
Já para as válvulas de controle e PSV’s, pode parecer que obtivemos um valor baixo para as médias dos dois projetos apresentados, mas é possível ver que isso depende muito de cada folha de fluxograma.
Se por um acaso em vez de duas bombas (que a princípio estão redundantes) houvesse outro trocador de calor, por exemplo, é bem possível que a média de válvulas de controle e PSV’s teria atingido a média dos projetos de metanol e triclorossilano.
Conclusão
Pudemos hoje por à prova e ver na prática quantas válvulas é possível esperar em uma folha de fluxograma de engenharia.
Vimos que esse número depende fortemente do tipo de equipamento que está ou não presente em cada folha, das utilidades utilizadas como fluido de troca térmica ou de limpeza, e de qual tipo de válvulas estamos falando.
Da próxima vez que precisar estimar o custo com sistemas de tubulação, use este post como referência e você já terá obtido um resultado bem preciso em relação ao tempo necessário para calculá-lo.
Até mais!